Metal Finishing
Give metal a strong, protective finish.
Higher production speeds and more complex design place increasing demands on the surface systems used in the manufacturing process. In addition to excellent corrosion resistance and decorative properties, factors friendly to the environment, such as the substitution of conventional release spray, are gaining importance. High-performance, reliable coatings improve cycling times, drastically reduce the cleaning requirements and help to increase productivity in production. Zekko offers its customers a wide range of surfaces with different or combined properties:
- Excellent Chemical and Corrosion resistance properties
- Good sliding properties
- Extreme resistance to wear
- High temperature resistance
- Powder Coatings resist cracking, peeling, and chipping.
- Powder coatings are abrasion resistant.
- Powder coating is durable and long-lasting.
Our quality metal finishing services can help to not only add colour to metal surfaces but to help protect them against corrosion and oxidation as well.
Powder Coating
Powder coating is an advanced method of applying a decorative and protective finish to a wide range of materials.
The powder used for the process is a mixture of finely ground particles of pigment and resin, which is sprayed onto a surface to be coated. The charged powder particles adhere to the electrically grounded surfaces until heated and fused into a smooth coating in a curing oven.
The result is a uniform, durable, high-quality, and attractive finish very resistent to scratches, cracking, peeling, UV rays and rust. Powder coating is the fastest-growing finishing technology.
We have a versatile Powder Coating Plant which allows us to coat mild steel, stainless steel, aluminium and galvanised product.
All Powder Coat items are blast cleaned, or swept blast in the cases of stainless steel and galvanised pieces.
Testing has taken our Powder Coat system in excess of 1000 salt spray hours.
Successful Powder Coating is all about the preparation.
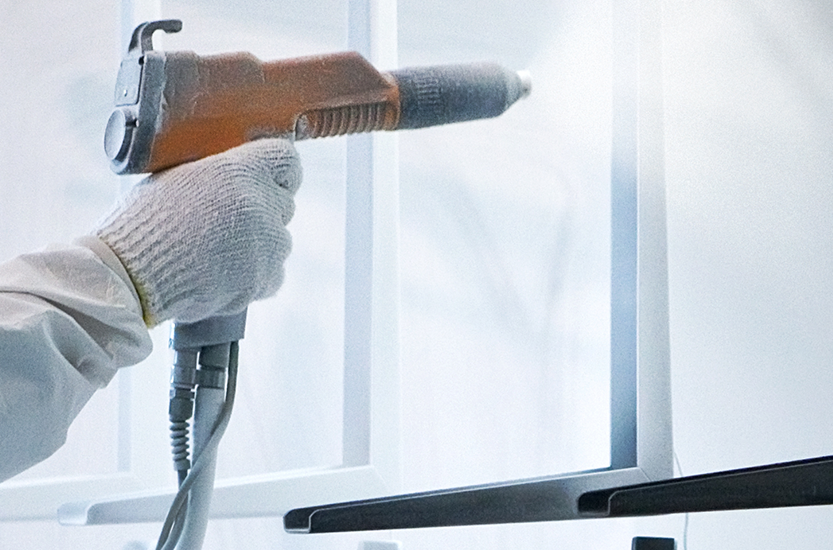
Why powder coat instead of wet paint?
Let us take the headache of painting your parts out of your hands. Why powder coat instead of wet paint?
- Economics – The economic benefits of powder coating are numerous but the largest benefit is due to efficiency and overspray. The average transfer efficiency of powder coating is 60-70% compared to liquid paint at a transfer efficiency of 30-35%. Plus, roughly 50% of wet paint product disappears through evaporation. The base product for powder coating is also substantially cheaper than wet paint.
- Safety – We can more safely apply our powder coatings than you can apply a wet paint. Powder coatings are inert, meaning they pose no safety hazards when not being sprayed. In addition, powder coatings do not contain harmful chemicals such as solvents or volatile organic compounds (VOC) that are often found in wet paint.
- Environmental – There are many environmental advantages of powder coating as well. Since there are no solvents or VOCs there is no damage to the environment during application. The waste is also not hazardous and can be disposed in the landfill. Wet paint contains harmful chemicals that have been proven to deplete the ozone and produces hazardous waste that needs to be disposed of in an appropriate manner.
- Mechanical – Powder coating generally produces a coating twice as thick as standard paint. This makes its durability much higher than standard wet paint. In addition, its flexibility and ability to bend and yield with the material is much better than paint.
Modern protective powder coatings offer excellent corrosion and UV protection and can be acquired in any color you need.
Looking for powder coating services in Chennai? Call us today at +91 95 000 96 374. We look forward to hearing from you.
Colors and finish
Zekko's Powder Coating – stocks a wide range of standard colours and finishes
Zekko's Powder Coating stocks a wide range of standard colours and finishes from world leading suppliers including Interpon, Jotun and Asian paints powder coatings. Specialty colours, finishes and other powder manufacturers products including Marpol and Lakshmi coats are also available upon request.
Physical colour samples of our stocked colour range are available in store for you to view and take home to colour match against any existing finishes you may have. Finish options include Gloss, Satin, Matte, Pearlesent, Texture, Ripple, Hammertone, Clear Coats, Tinted Clears, Anti-graffiti coatings and more. If the standard powder coat colour range does not meet your requirements, custom colour matching and powder manufacturing is also available on request.
Please click through to our supplier websites using the linked images below to view the full range of powder coat colours and finishes available. NOTE: When viewing the Interpon colour range linked below, please apply the 'Stock' Availability filter option for the most cost effective colour range to select from.
Powder Types
Powder Coating – powder types
Not all powders are created equal. Some chemistries perform better than others against certain environmental criteria. So, it’s important to know how the product will ultimately be used before selecting the type of powder for application.
Epoxy Powders
Epoxy coatings provide a smooth, uniform appearance. They also offer excellent adhesion and exhibit a strong resistance to chemicals and corrosion. However, epoxies can only withstand minimal UV exposure. Over-exposure to UV rays can lead to loss of gloss as well as chalking of the finished product. As a result, epoxy powders are generally used for interior-based products.
Polyester Powders
Polyester powders offer strong adhesion properties and excellent gloss retention when exposed to UV elements. Due to their strong weathering characteristics and lower chemical resistance, polyester powders are typically found on fencing, outdoor decorative items as well as lawn and garden furniture.
Nylon Powders
Nylon powders are generally used as a protective coating. They offer strong resistance to a wide range of solvents and oils, as well as damage caused by impact and abrasion. In most cases, a primer is used in the coating process to help achieve a high level of performance.
Polyurethane Powders
Polyurethane powders are generally used for both decorative and functional products that have exterior exposure. Polyurethane's have very strong weatherability characteristics. They offer excellent anti-corrosion performance and are resistant to humidity and a range of chemicals and oils.
Hybrid Powders
Hybrid powders are blends of epoxy and polyester resins. As such, they offer excellent mechanical properties and very good chemical and corrosion resistance. While these coatings provide excellent flexibility and smoothness, they are generally not recommended in applications where weather resistance is critical. Hybrids are typically used for indoor applications.
Metallic Powders
Metallic coatings are offered in a variety of chemistries from epoxies and polyesters, to hybrids. These coatings have metallic particles added to the chemistry of the powder for aesthetic purposes. Their highly attractive visual attributes combined with their strength and durability make them an ideal choice.
Metal pre-treatment
A Phosphate Pre Treatment adds significantly to the performance of the finished coating.
Pre-treatment is the essential preliminary stage where metals are prepared prior to electrostatic powder coating. This cleansing process removes any residual dirt, oil and contaminants and prepares a suitably conductive surface to receive the electrically charged paint particles. A phosphate coating converts the metal substrate to a uniform, inert surface, which improves bonding, minimizes the spread of oxidation if the coating is scratched and improves the over-all resistance of the component. This enhances the coating adhesion and strengthens the durability and corrosion resistance of the powder coating finish.- Imparts greater corrosion resistance
- Offers a measure of galvanic protection
- Protects in the event of a scratch
- Prevents filiform & undercutting corrosion
- Works as a primer
8-STAGE PRE-TREATMENT WASH
While three-stage and five-stage wash systems are most common among custom coaters, Zekko Integrated Systems & Solutions has gone the extra mile and equipped its facilities with a robust eight-stage pre-treatment, automated transporter system to enhance the long-term performance of your product.
This superior eight stage system was designed to ensure that our customers' products are properly cleaned and free of oils, lubricants and other impurities prior to painting. Topped with a re-circulating rinse, our customers can be confident that their product has been properly cleaned for a superior finish.
Our entire wash system is controlled. Temperatures, tank levels, pressures, motors, pH levels and conductivity are monitored closely, at all times, to ensure the performance of all eight stages is optimized - giving your product the ultimate cleansing experience.